SynErgie Satellite Projekt
How the DisConMelter project has made molten glass more flexible
DisConMelter was a satellite project of SynErgie that ran from 2016 to the end of August 2019. Both projects pursued the same goal: to adapt industrial processes so that they can consume more electricity when more is currently available in the power grid, and reduce consumption when there is a shortage. However, DisConMelter dealt exclusively with the glass industry.
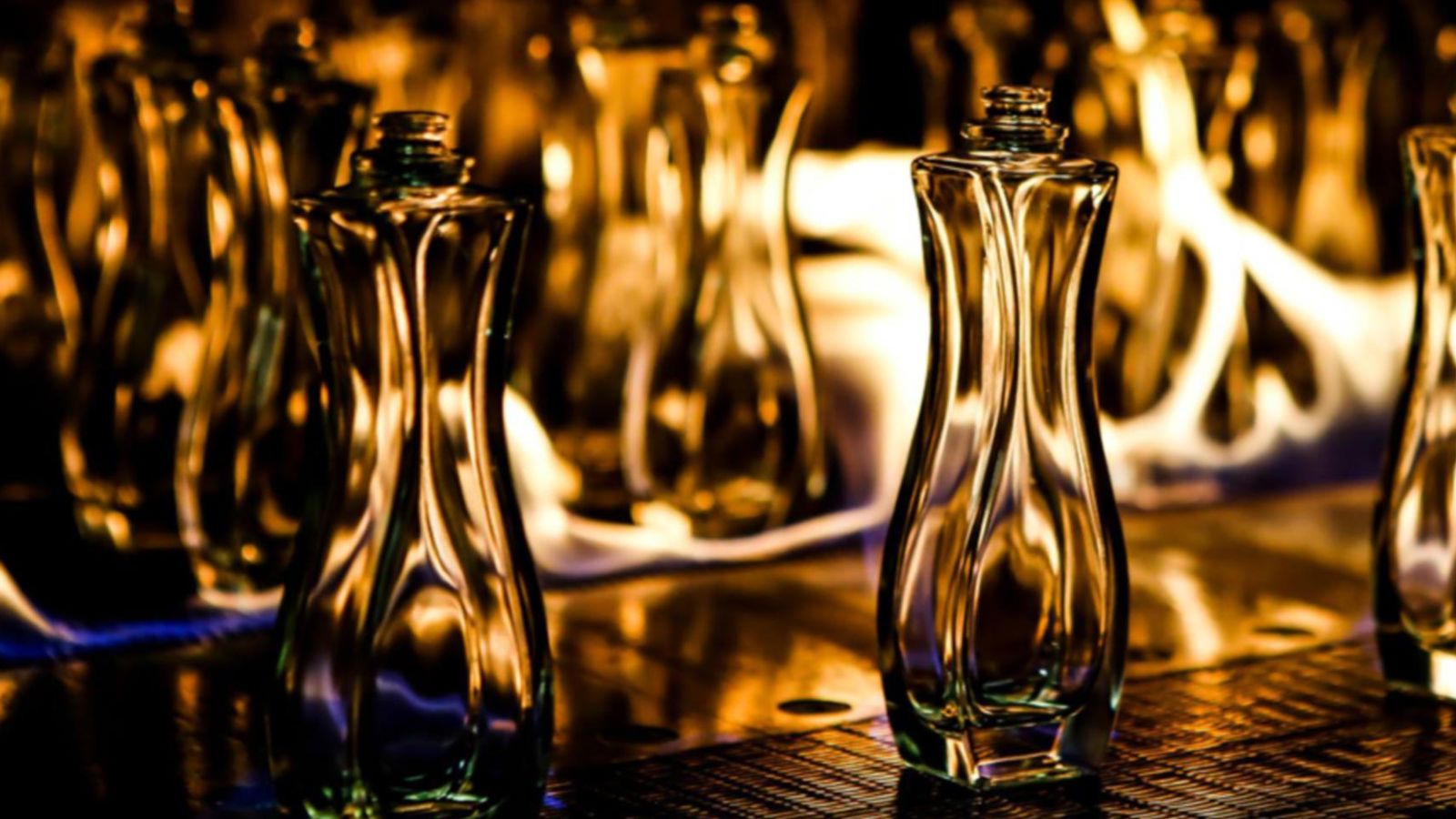
Germany is Europe’s largest glass producer, with almost € 2 billion in turnover. However, to date glass production has been dependent on burning fossil fuels to melt quartz sand, lime, and soda at around 1400 °C to produce the glass.
The DisConMelter, an electrically operated melting tank, intended to change that. Glass-melting tanks are designed to provide a constant temperature and filling level. The project of the same name focused precisely on this area. The goal was to build a smelter consisting of three modules that separated the production steps, which had previously immediately followed each other, since this was the only way to facilitate flexible energy consumption in glass production.
Module 1 melted the glass. The glass would only be melted when there was more electricity available on the market than was actually needed. The molten glass was then transported to module 2, a huge reservoir capable of storing the liquid glass for a long time with minimal energy loss. Unlike with the glass-melting module, energy consumption for the glass reservoir was flexible. This meant that it could operate for a certain amount of time with greater or lower power consumption. The liquid glass stayed in the glass reservoir until there was enough excess electricity once again. Finally, module 3 was responsible for processing the glass to produce tubes, bottles, and drinking glasses.
Separating the molten glass into three steps has two major advantages. One is that glass can be produced with flexible energy consumption. Because the glass industry consumes huge amounts of electricity, companies in this sector could stabilize the power grid to a considerable degree in future by using this new procedure. The other advantage is that the modular system, if implemented on an industrial scale, could also benefit employees. Existing glass smelters do not allow for any interruptions to production – the machines operate day and night. The ability to temporarily store the glass and shut down the smelting process could dispense with the need for night and weekend shifts in glass production in future.